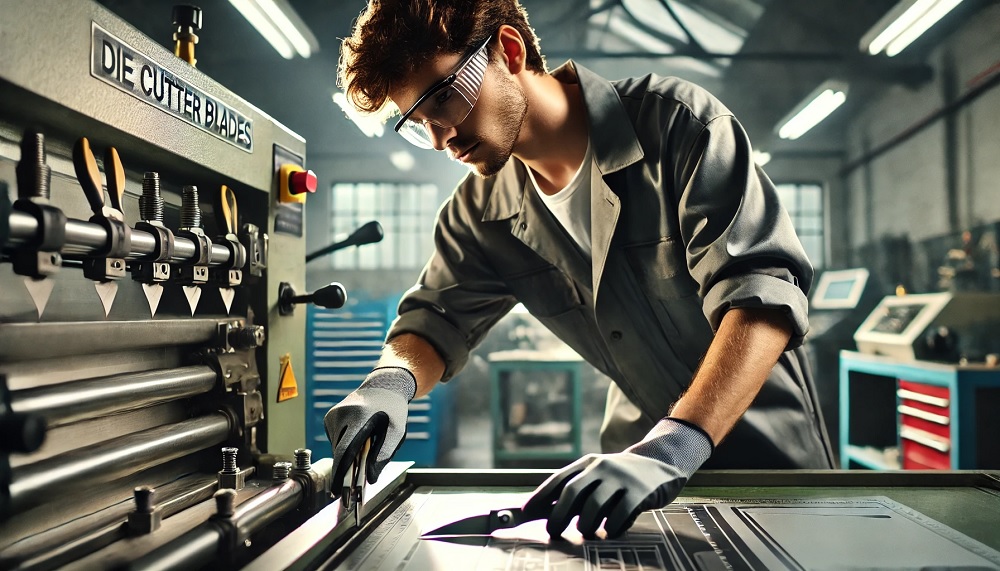
Achieve Precision Cutting with Top-Quality Die Cutter Blades
Die cutting is a common procedure used in the printing, packaging, and metalworking industries that entails chopping, forming, and shearing sheets of stock material into unusual forms and patterns.
Just as a cookie cutter forms the dough into a precise shape, a die also shapes metal or other materials into the required form. Before the label is removed, the die removes the surplus material or matrix. The ‘die line,’ which is usually a thick, coloured line in proofs, is the contour of the area that the die will cut.
Manufacturers may swiftly and effectively create a large number of identical products by utilizing a die, which is a specialized instrument intended to cut a particular form. For example, die cutting in the printing sector makes it possible to create distinctively shaped labels that give items a little extra personalization.
What Are Dies?
Metal words, letters, or patterns called dies are used to carve images out of materials. They are different sizes and shapes.
Several Kinds Of Dies Are As Follows:
- Nesting Dies: These dies are available in various sizes and feature a standard design. Every die in the set is marginally smaller than the last, resembling a series of nesting dolls.
- Corner Dies: Detailed designs can be created by positioning these dies in the corner of the material. For creating artistic scrapbooking borders, they are perfect.
- Edge able Dies: These dies follow the edges and are similar to corner dies. They work wonderfully for incorporating distinctive elements into the border of a greeting card or present box.
Various Die-Cutting Techniques
- Blanking: This method further slices the material by trimming its outer borders. The material is already flat.
- Drawing: The material is pulled to the required length by the machine. Usually, long and thin objects are handled with this technique.
- Forming: On a curved surface, the raw material is formed. Custom cylindrical packaging components can be made with this technique.
- Coining: The material is compressed to form circular holes, which provide elaborate packaging designs.
- Broaching: This technique strips the material with a steel die that has several rows of “teeth” on it.
Die Production Process
Steel rule dies are a major component of die cutting. More than 150 years ago, dies were hand-carved and placed into wooden blocks; nevertheless, automation and increasing efficiency have helped modern die production.
- Design: The die’s layout is made using computer-aided design (CAD) software. Precise measurements are obtained by carefully reviewing pertinent factors and dimensions.
- Foundation: The flat base of steel rule dies is composed of metal or wood. Rotating die bases are made of curving metal or wooden components that either sit on top of or are made of metal cylinders.
- Plasma Cutter: A laser is used to cut a pattern into the base material for inserting the steel blades into a flatbed die cutter. Before the die cutter blades can be mounted, kerf cuts, sometimes referred to as precision cuts, are required.
- Blade Forming: By programming CNC machines, the exact kerf shapes required to complete the blade shaping can be produced. A revolving die has its cylindrical surface inscribed with the die.
- Ejection Rubber: The die has an ejection rubber strip that makes it easier to remove the cut piece without damaging the material or allowing it to fray, tear, or adhere to the steel rule while being cut.
Conclusion
Steer clear of sharp edges and angles to avoid ripping the matrix during removal following die cutting. If your label has a hole, make sure there is space between the hole and the edge of the label to prevent tearing. Make sure that the artwork utilized in the label’s design extends at least 1/16″ past the label’s boundaries. This will prevent the accidental insertion of blank spaces.